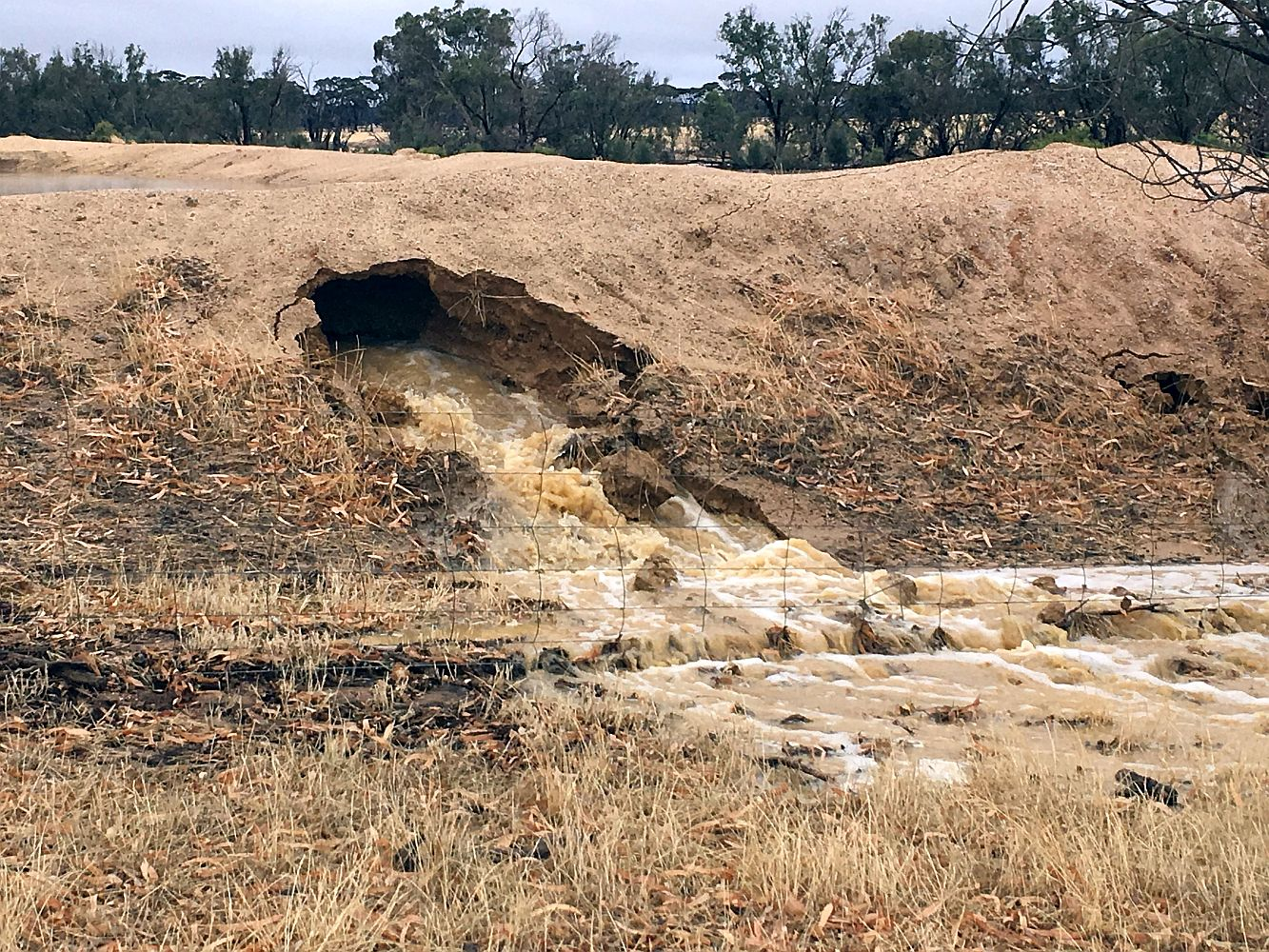
How to know if your dam is leaking
It could be obvious and continuous:
- water flowing in never seems to fill it properly
- water seeping through the walls
- rushes growing around the base
- the dam empties out much faster than evaporation or use should indicate.
Or it could be insidious and only shows up sometimes:
- water level drops slightly faster than evaporation or use should indicate
- vegetation or pastures and crops below the dam healthier than elsewhere
- leakage increases after sudden inflows from summer storms.
Other likely indicators are the soil type in the dam:
- red loamy soils and soils with broken rock are more likely to leak.
Why is your dam leaking?
The most common causes are either poor construction, or storm damage. Storm damage commonly breaches an entire wall when the spillway system cannot cope with the volume of water flowing into the dam. In a 2017 summer storm, fresh water inflows to dams holding brackish water led to tunnelling of dispersive clay linings, and caused major leaks.
Common construction problems resulting in leaks are:
- failing to remove topsoil and vegetation from the embankment site
- not having a proper cut-off trench under the embankment
- using unsuitable soils for the embankment and dam lining
- poor soil compaction – this is one place where you want compacted soil with poor structure
- failure to seal exposed rock, gravel or sand in the storage basin.
See the Excavated earth tanks (farm dams) page for detailed information about planning, designing and constructing farm dams.
What you can do about leaky dams
First, decide if it has to be fixed. After filling the dam, if water loss is minor, there is still usable water in the dam at the end of summer in most years, then it is probably not worth the possible large expense of preventing leakage.
If water loss is substantial, there is little or no usable water in the dam at the end of most summers, then your options are:
- build a new dam in a suitable position with suitable soils. In many cases, this will be the best option, because it also allows construction of better water harvesting systems (preferably a roaded catchment) to allow for changed land use and climate change, and the cost of other options can be too high for the result. This option is probably the best one.
- add a plastic membrane liner in the dam when the dam is empty
- compact soil in the dam when the dam is empty. This may help if there is enough clay in the soil, and the right machinery is available.
- blend and compact soil in the dam when the dam is empty. This removes leakage seams and gives a more even lining to the dam.
- success is about 50%
- costs about one third to two thirds of the cost of a new dam.
- add a local clay liner in the dam when the dam is empty.
- success is about 80%
- cost may be one and a half to 3 times the cost of a new dam.
- add a bentonite clay liner in the dam when the dam is empty.
- success is about 50%
- costs may be about 2 to 3 times the costs of a new dam.
- add sealants to the water in the dam when the dam is full, or to the dam lining when empty. Depending on the leakage type, this can be with gypsum or sodium tripolyphosphate (STPP).
- success rate is low, may increase leakage in some cases, and needs repeating every few years.
Successful treatments are often costly, and if another dam site is available, constructing a new dam may be the cheapest and more effective option. Sealant treatments normally require that the dam is empty to increase the likelihood of success.
Adding sealants to the water in a dam rather than directly to the underlying soil appears simple and relatively inexpensive, however the resulting application rates are uncontrolled and the success rate is lower. The treated layer, which remains at or near the soil surface, is not compacted, and may be easily disturbed and damaged.
There is an occupational safety risk with some of these treatments: Steep batter slopes in dams are safety hazards for operators of earth-moving equipment. Trained, experienced personnel should supervise all operations.
Building a new dam may be your best option
Leaking dams may be expensive to treat, with no guarantee of success, and are often not in the best locations after decades of changed land use and changed climatic conditions. We recommend revising a whole farm water management plan before making large financial commitments.
Farm dams are most effective at holding water when the base and inside walls of the dam are sealed with clay of low permeability to minimise leakage, and where catchments are improved to increase and collect run-off. In many agricultural areas of WA, natural run-off from crop land and pasture is not adequate to reliably fill farm dams. Run-off can be improved by using roaded catchments or well maintained grade banks.
Site preparation for dam sealing
To prepare for dam sealing:
- divert inflow during installation of the dam liner and the inlet structure
- pump all water from the dam; remove silt and organic matter down to the level of the original dam floor; smooth any rills and gullies
- if a lining layer is to be installed, compact any fresh soil-fill in the gullies
- allow for inflow to enter the lined dam via a stable inlet (generally requiring an embankment or silt trap across the open front of the dam to direct inflow to the inlet structure).
- if possible, fill the dam slowly (30 cm a day) to allow for proper wetting of the lining material, and gradually increase load on the embankment.
Options for leaky dams
The best available membrane lining materials are polypropylene and high-density polyethylene (HDPE). Both are suitable for storage of potable water, and both materials can be stabilised to reduce the effects of ultra-violet radiation, and therefore do not require a protective soil covering.
What are the differences?
- The manufacturers indicate that when installed to specification, an exposed liner of polypropylene 1 mm thick has a life expectancy of at least 17 years, and an exposed liner of 1.5 mm HDPE has a life of 20 years.
- HDPE is comparatively inflexible; requires a very stable and smooth foundation; and is fabricated in-situ. Polypropylene is more flexible, can often be prefabricated, and is suited to sites where some foundation movement may occur, and where a smooth surface cannot be guaranteed.
Costs and success estimates
Supply and installation of 1 mm polypropylene costs approximately 25% more than 1.5 mm HDPE. Because polypropylene is manufactured in Australia and HDPE is imported, the price differential between the two materials is not constant.
The price differential per m2 is largely offset by the cheaper foundation preparation for polypropylene. The two membrane materials are therefore regarded as equivalent-priced options, and the choice depends on site conditions. The success rates for both are greater than 90%.
To achieve optimum compaction, soil moisture content should be at or near to the optimum: 36–20% for highly plastic clays; 24–12% for most clays and silty clays (FAO), and the maximum soil layer thickness should be 200 mm. At the optimum, it should be possible to roll the soil between the palms of the hands to form a pencil-thick rod without breaking. If the ‘pencil’ of soil breaks, the soil is too dry, and water should be added to make the soil more plastic.
Compaction is best done with a roller of adequate weight and power (e.g. a self-propelled pad-foot roller). Although track rolling with a dozer is unlikely to achieve similar soil densities to those obtainable with the correct machinery, it is still valuable. Livestock, particularly sheep, can apply significant compaction at the water line when drinking from a dam.
As the water level drops over weeks to months (depending on season), sheep traffic can break down soil structural units, and may help to reduce seepage loss.
In the agricultural areas of WA, the soils in the floor and lower walls of excavated earth dams often exhibit structures similar to the fabric of the parent rock from which the soil has formed. The subsoil may consist largely of massive, dense clay blocks, which are occasionally separated by quartz-rich veins and fracture lines through which water may move rapidly. Blending of these soil materials by ripping, mixing, stockpiling, replacing in layers, and compacting, can sometimes solve a leakage problem.
Costs and success estimates
The estimated cost of blending and compacting the floor and lower walls of a dam ranges from one-third to two-thirds of the cost of a replacement dam, and has about a 50% chance of success.
When a source of suitable clay is available near a leaking dam, placing that material as a compacted soil blanket can seal a dam successfully and economically.
Basic soil suitability criteria for a clay blanket are:
- 20%-40% clay content
- uniform particle size distribution i.e. well graded soil
- slight to moderate soil dispersion
- low to moderate linear shrinkage
- kaolinite-dominant clay mineralogy.
Strict specification of the soil materials used, the level of compaction, the thickness of the sealing layer, and a protective soil layer on all batter slopes, result in this method being as expensive as a flexible membrane liner. A 1 m thick compacted soil blanket is recommended to reduce seepage to a maximum of 2 mm per day.
Costs and success estimates
Such a blanket occupies a significant volume in a small farm dam, and prior to placement, excavation to compensate for the loss of capacity will be an extra cost. The estimated cost of placing a 1 m thick compacted clay blanket with a minimum 92% of maximum dry density is one and a half to 3 times the cost of a replacement dam. The likelihood of success is estimated to be 80%.
Bentonite clay expands to several times its dry volume on wetting, and is therefore suitable to reduce the rate of water movement through porous soil.
Clay selection
The highest grade (with the greatest swelling characteristics) is sodium bentonite. Calcium bentonite swells less than sodium, and is potentially less effective for dam sealing.
Impurities such as calcium and magnesium carbonates and quartz reduce effectiveness, and the fineness of grinding and screening affects the ease of mixing with other materials. Watheroo calcium bentonite is commercially available at several centres in the agricultural areas of WA. The product is sold unscreened in bulk, and screened in bags.
All sodium bentonite available commercially in WA is imported from the eastern states or overseas. Laboratory comparison of a high grade sodium bentonite and the Watheroo calcium bentonite has shown that the sodium bentonite has significantly lower capacity to transmit water.
Application
Bentonite can be applied either as a mixed blanket or a pure blanket. A pure blanket is recommended if thorough mixing with the underlying soil cannot be achieved. Less bentonite is required in a well-mixed blanket than in a pure blanket, to provide a sealing layer of a given thickness (e.g. 10 cm).
Laboratory tests indicate that equal thicknesses of a 50:50 mix of bentonite and soil and pure bentonite have similar hydraulic conductivities or ability to stop seepage.
In a mixed blanket, bentonite is spread on the soil surface then mixed thoroughly into the top 10 cm of soil using a rotary hoe, followed by compaction of the moist bentonite-soil mixture. A protective layer of non-erodible soil should also be applied and compacted.
As a pure blanket, bentonite is spread uniformly over the soil surface to form a continuous sealing layer that is covered by a protective layer of non-erodible soil. The protective layer should be compacted.
The required thickness of the sealing layer will depend largely on:
- type of bentonite
- ratio of bentonite to soil
- uniformity of bentonite application.
Application rates vary considerably depending on the local conditions. As a guide, we suggest:
- high grade sodium bentonite – 15 kgs/m2
- Watheroo calcium bentonite – 60 kgs/m2.
Costs and success estimates
Based on these rates, the cost of installing a mixed blanket of calcium bentonite in an average-sized farm dam is approximately 2 to 3 times the cost of dam replacement. The likelihood of reducing seepage to less than 2 mm per day is estimated to be 50%.
Sodium bentonite is also available as a prefabricated liner consisting of high grade bentonite impregnated into a fibre mat. Due to the need for specialised installation equipment and high cost of the mats, they are not generally suitable for farm dams.
‘Piping’ or tunnelling through a dam wall or embankment occurs when water seeping along a line of weakness creates a ‘pipe’ or tunnel. The line of weakness may be because of failure to seal exposed rock, gravel or sand in the storage basin, or dispersive clays cracking when dry and allowing water to breach the lining.
Soils that are dispersive, high in clay and exhibit severe cracking on drying are prone to piping. If an embankment dam fills rapidly, water may leak along crack lines in the relatively dry embankment, and the crack lines can develop into pipes or tunnels as the dispersed soil is carried away by water flowing through the rapidly enlarging cracks. Minor piping failure in dispersive soils can be treated with gypsum after the pipes and crack lines have been sealed.
Gypsum
We do not recommend adding gypsum to water in the dam to treat existing leakage.
Gypsum soil treatment
Gypsum reduces dispersion, and can be used on dams constructed with dispersive clay soil lining where:
- the leakage is minor
- after the crack lines or small pipes have been sealed by soil blending and/or compaction.
The treatment process is:
- drain the dam to expose the problem embankment
- add finely ground gypsum to the drained-dam embankment during reconstruction at the rate of 1% by weight, or 4 kg/m2 to treat the top 200 mm layer of soil
- blend and compact the top 200 mm of soil in the embankment.
The likelihood of successful treatment is about 80%.
Gypsum water treatment
This is not a preferred way of treating potentially leaky dams. Piping failure is more likely when the dam empties and cracks appear above the waterline, then refills with fresh water. In this case, use the treatment process in the section above.
Where there is no current leakage, the water level rarely drops, and there is potential for leakage in dams constructed with a dispersive clay lining and holding fresh water, gypsum can be added to the dam water at 1 kg per 10 m3 of water volume.
Even application across the surface of the dam can be difficult. The likelihood of successful treatment is estimated to be about 50%, and repeat applications will be required every 2 or 3 years depending on water quality.
Sodium tripolyphosphate (STPP)
We do not recommend using STPP in leaking dams unless experts are available to specify, design and supervise the project.
Some soils used in dam construction – mottled zone and some pallid zone soils – are naturally porous and have low levels of leakage. Reduced seepage results from the collapse of the soil structural units and subsequent blocking of soil pores due to increased mobility of soil particles.
Do not use STPP where dam leakage is from seepage spots that may indicate potential piping failure. In 20% of treated dams, the supervised application of STPP at recommended rates has led to greatly increased seepage due to induced piping failure.
STPP increases dispersion and can be used to seal dams:
- constructed of mottled zone soils and pallid zone soils
- where the leakage is minor
- after lines of weakness have been sealed.
STPP is a powerful dispersing agent which is a common ingredient in washing powders. At recommended rates and methods of application, STPP can reduce the seepage rate from leaking farm dams in mottled zone and pallid zone soils.